Prepping the recovery system. This was one of Jaime's favorite shots.
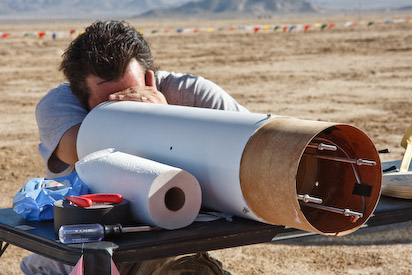
Connecting the electronics board
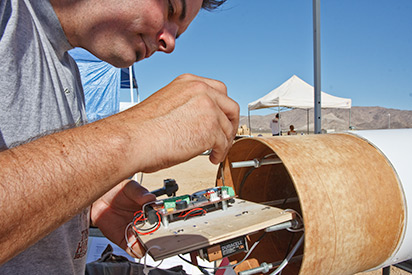
Stuffing the Rocketman 16 foot chute into the deployment bag is much easier than folding. Very cool system
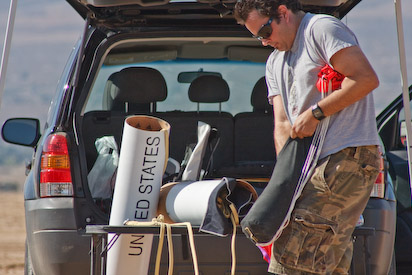
That's a big motor... It's 3" in diameter, almost 2 feet long, and weighs 9 pounds!
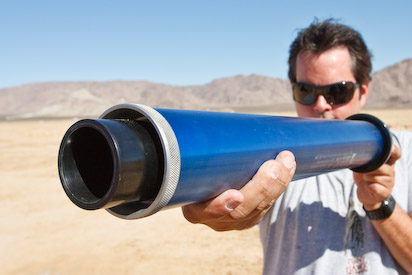
Artsy shot
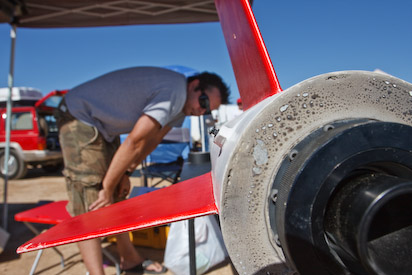
Here I'm trying to hold the almost 10 foot long assembled rocket at 51.1 pounds
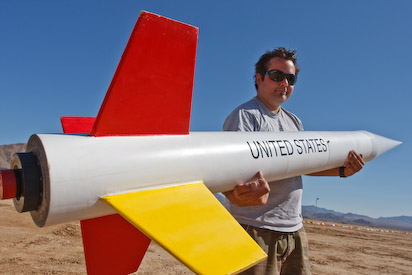
Everything's ready to go. It was a tad windier than I would have preferred but it caused no problems
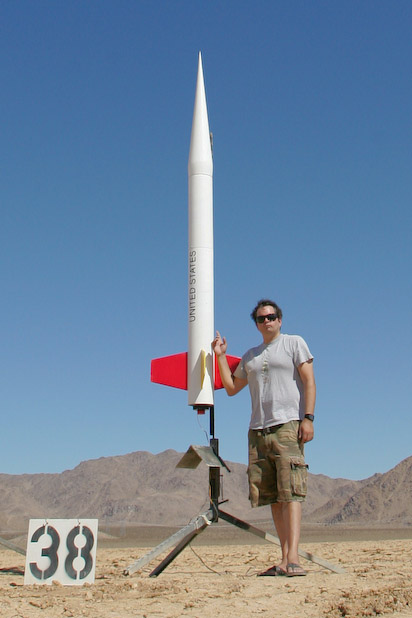
Jaime set up my Canon 1D mark II at a very low angle with a wide lens. From this vantage point he captured some very cool motor details
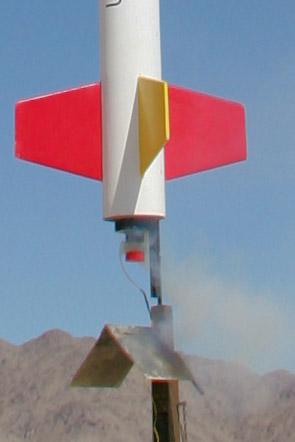
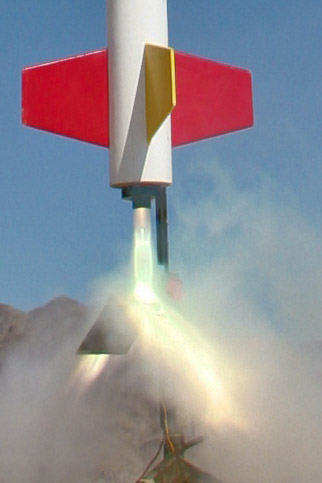
Here's the low angle flight shot. Note the blast debris coming right for the lens. The UV filter was filthy!
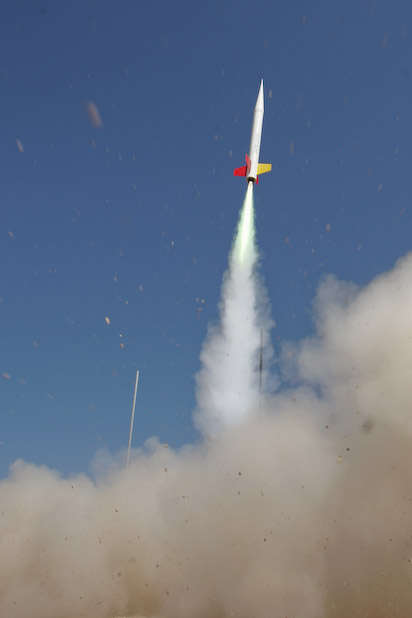
Jaime shot this handheld with the 300 mm f/2.8 lens. I'm surprised how angled the flight appears here because it straightened out for the remainder of the flight. This motor kicks ass and the 51.1 pound beast really bolted into the sky:
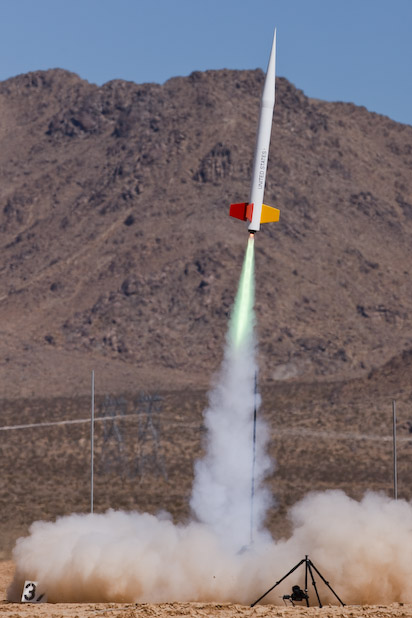
This is a tiny crop of another handheld 300mm shot. You can see the chute has dragged out of the deployment bag:
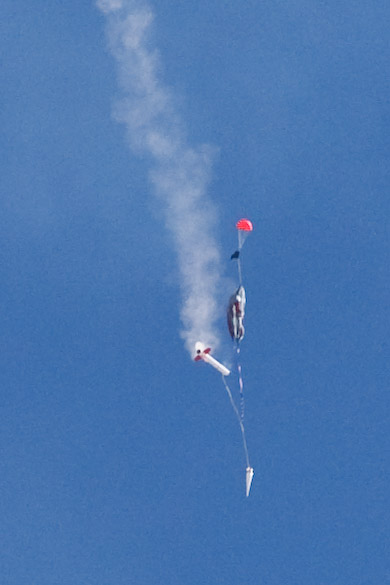
Here the chute has just fully inflated. Everything's looking good.
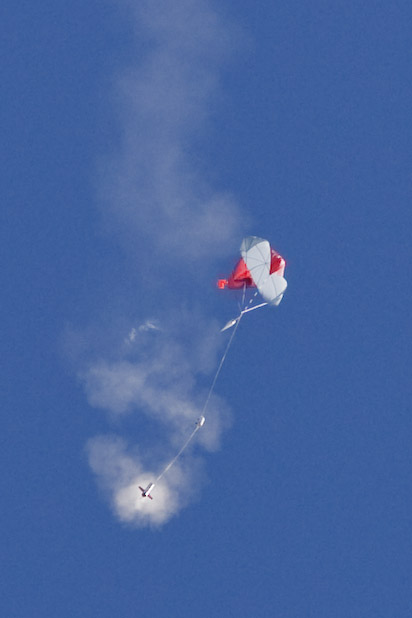
I was quickly walking initially to keep up with the descent. As the rocket decreased in altitude it became obvious that the winds were at lower altitudes so I had to start running to prevent the chute from dragging the rocket along the lakebed after touchdown. Jaime hit the deck to catch this cool shot

That's 65 feet of Kevlar stringing all the goodies together
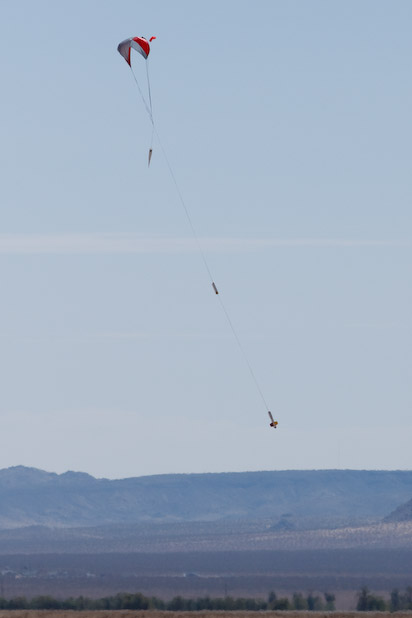
Here I've fully inspected the rocket and everything's intact. Victory!
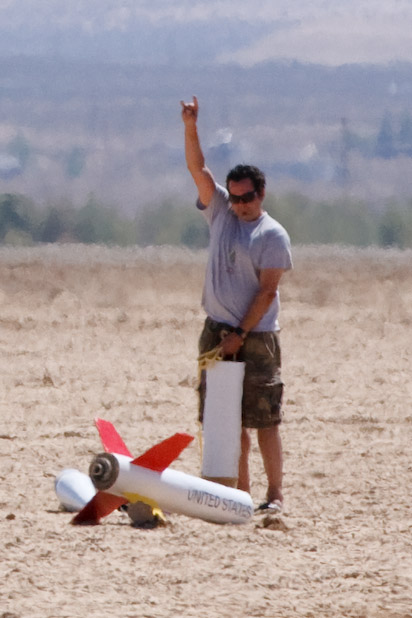
Dok and Kurt signing off on my level 3 paperwork
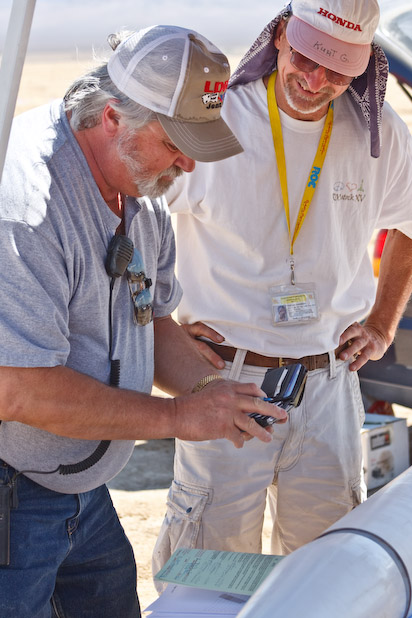
Here's the performance data from the AltAcc2C altimeter
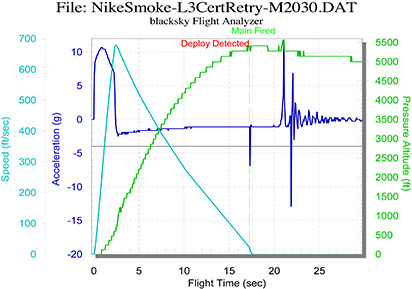
And the data from the ARTS2 altimeter
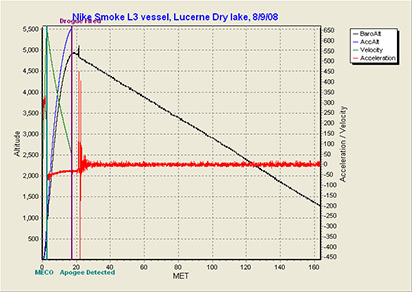
Finally here the motor analysis from the ARTS2. I'm not clear on why that spike occurred early on. Perhaps a propellant chunk shredded off and clogged the nozzle?
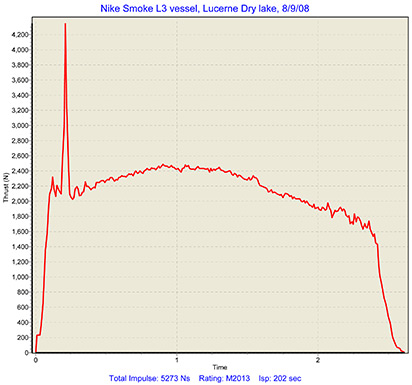
I want to thank Jaime for trekking out there with me and shooting photos. I couldn't have done this without his help. Also a big thanks to my TAP members, Dok Hanson and Kurt Gugisberg. I appreciated their kind assistance and patience. Finally thanks to Jack Garabaldi of What's Up Hobbies for lending me his motor casing and for his unparalleled dedication to this hobby.
What's next? Well I spoke to Dok and Kurt and expressed my interest in becoming a Tripoli TAP member for the San Diego club. Right now Tripoli San Diego can only certify level 3 for NAR members so if I became a TAP that would make things easier for everyone. They encouraged me to fly a bunch more M motors, use a wide range of electronics, and to learn hybrid motors. At some point in the future it would be up to Dok and Kurt to recommend me as a TAP member so I'll continue to work on my rocketry "résumé."