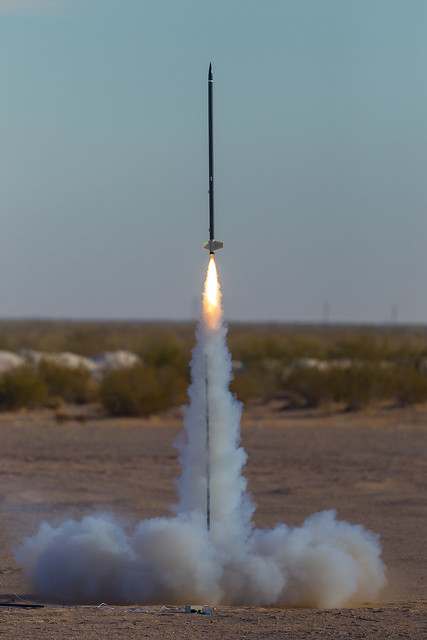
...but there were several issues during prep and the primary reason for the flight, the cable cutter test, failed. This was the first flight of what was supposed to be a super robust, carbon-fiber-overlaid, minimum diameter 54mm design. I built this very high aspect ratio rocket to take any 54mm certified motor but the K815, while cool, would not be pushing any aerodynamic limits that day.
I specifically designed and 3D-printed the black caps [below] to fit in this rocket's electronics bay and cut a length of 1/4-20 all-thread that morning to hold the caps in place. However, upon assembly, I discovered that the all-thread rod was ~2" too short. I still have no idea how that happened as I'm somewhat familiar with ruler use. I was about to give up but this was my only planned flight for the day so I quickly decided to shorten the already too long coupler to fit the all-thread assembly. I bought a DC Dremel tool and that made quick work of the modification.
So now everything fits together as originally planned and the rest of the prep goes relatively smoothly. The booster segment is only 36" long so a K185 with even a shortened coupler doesn't leave much volume for the recovery goods. With Darrell's help I was able to get everything packed in and two pieces of masking tape seemed to hold the payload section into the booster.
Out at the pad I armed the Raven 3/Power Perch with the large magnet but rather than the expected "high high low low" dual-deploy beep pattern Darrell and I heard only "low low low pause high" (I think). I admitted that I had not powered up the altimeter after prep as a test but this setup always works as expected so I had become overly confident. In any even we agreed that something was wrong and pulled the rocket. We undid all the careful packing work and checked the connections only to hear the same odd pattern after several iterations. Once again I had planned to scrap the flight... defeatist! Coincidentally I started talking to Russ Sands afterward who offered that it sounded like my LiPo battery below a safe voltage threshold. I always charge my batteries the morning of a flight so I was skeptical but swapped to a different battery anyway. Lo and behold it powered up with the expected dual deploy beep pattern! Well done, Russ, and thanks for the input. I'll need to charge and test all my Raven batteries before the next launch.
OK so I crammed everything back together, got the rocket on the rail, armed the Raven 3, and loaded up the stock AT igniter. Darrell was kind enough to launch for me but there was no ignition on this first try. I've always found these Aerotech 54mm moonburners difficult to ignite and should have proactively metered some thermite. Instead I used one of my older, dipped igniters on the second try. There was a small puff of smoke upon ignition and then about 10 seconds of smoldering before the motor finally pressured up. I was a bit worried about the moon burning thrust vector and minor curvature in the 4' long payload section but did everything I could to balance those forces during prep. Ultimately the ascent was straight, true, and out of sight. I used a 12g CO2 cartridge at apogee so there was no visible event at the top. Luckily the Comm-Spec tracker signal boosted once the antenna was free from the carbon fiber shell so I knew I had separation. Darrell and I walked right up to the rocket about 1/3rd mile away using the tracker. Everything had separated but the main parachute's "burrito" remained intact with the cable cutter still in place. D'oh!
I suspect that some of the BP leaked out of the cutter's cylinder despite a relatively thick wire to the ematch. I had used a sealing o-ring around the wire in the previous night's test but it didn't seem to fit over the black wire I used for the flight. Just in case I had plugged the cap with wall-tack clay but apparently that didn't help. I suppose I'll force the o-ring over the wire next time and the new MTek leads are of apparently smaller diameter.
The bottom ebay cap had hit the ground and cracked another inch off of the coupler despite internal carbon fiber reinforcement. This impact also knocked the baro sensor off the Raven 3 and I have yet to be able to power it back up. I might try to have it fixed but, with two abusive flights on it, the unit could be dead. Good rocket science-y times!